Table of contents
The manufacturing industry is constantly evolving, with companies seeking ways to enhance efficiency and cut costs without compromising quality. Refurbished CNC lathes and milling machines have emerged as a cost-effective solution to breathe new life into production lines. This write-up delves into the rejuvenation of productivity through these revitalized tools, shedding light on their practical benefits and strategic importance. Continue reading to understand how integrating refurbished machinery can be a game-changer for your manufacturing processes.
The Economic Advantage of Refurbished Machinery
Purchasing refurbished CNC lathes and milling machines presents a cost-effective alternative to acquiring brand new equipment. The initial investment required for refurbished machinery is considerably less, offering significant savings that can enhance the financial health of a manufacturing operation. By opting for refurbished lathes savings, businesses can expect a quicker Return on Investment (ROI) due to the lower upfront costs. Furthermore, the reduced expenditure on equipment allows for the reallocation of business funds to other vital sectors, such as research and development or workforce training. This strategic redistribution of resources can lead to innovation, improved productivity, and a stronger competitive position in the market. In essence, selecting cost-effective CNC solutions in the form of refurbished machinery is a savvy economic decision that can yield tangible benefits for a manufacturing enterprise.
Environmental Impact and Sustainability
The manufacturing sector is increasingly embracing sustainable manufacturing practices, with companies opting for refurbished CNC equipment as a testament to their commitment to environmental stewardship. By choosing to reuse and repurpose CNC lathes and milling machines, these businesses significantly contribute to environmental footprint reduction. This approach not only conserves the resources and energy required to produce new machinery but also diminishes the waste associated with disposing of older equipment. The positive implications of CNC machinery repurposing are manifold, offering eco-friendly production solutions that align with corporate sustainability goals. The message is clear: by integrating such practices, companies not only optimize their production efficiency but also demonstrate a laudable responsibility towards the planet.
In line with these green initiatives, SAMO Machine Tools exemplifies a brand that aligns with the values of sustainability and reduced environmental footprint, providing an array of refurbished machinery that supports the industry's shift towards more conscious manufacturing processes. Their activities echo the growing consensus that the health of the environment is a shared responsibility, influencing the adoption of practices that ensure a greener future for all.
Ensuring Quality and Reliability
When it comes to revitalizing productivity with refurbished CNC lathes and milling machines, concerns may arise regarding the quality and reliability of such equipment. To alleviate these concerns, it is essential to understand that these machines go through a comprehensive quality assurance process. This includes a thorough inspection to identify any wear or defects, followed by the necessary repairs or replacement of parts to bring them up to speed. After the physical refurbishment, stringent equipment testing is conducted to ensure that each machine meets specific CNC performance standards.
The term 'refurbished' often carries with it a stigma of being second-rate or less reliable. However, this misconception fails to consider the rigorous processes in place to verify that quality refurbished CNC machines offer a level of performance that rivals their brand-new counterparts. Reliable milling machines that have been refurbished are not just patched-up versions of their former selves but are restored to a state that aims to match the original manufacturer's specifications. Customers can rest assured that refurbished machine reliability is not a matter of chance but a guarantee backed by meticulous testing and certification.
Integration and Compatibility
Introducing refurbished CNC lathes and milling machines into an existing production setup can be accomplished with minimal disruption, thanks to the inherent design of these machines for seamless CNC integration. It's vital to understand how these machines can complement and enhance current workflows without necessitating extensive overhauls. With an emphasis on production line compatibility, refurbished CNC equipment is often engineered to dovetail with both outmoded legacy systems and cutting-edge modern manufacturing technologies. This adaptability ensures that businesses can maintain production efficiency while transitioning to upgraded machinery. Moreover, the scalability of CNC technology means that as a business grows and its production demands increase, these machines can be scaled to meet heightened output requirements. This flexibility is particularly beneficial for companies planning for long-term growth and looking to future-proof their operations with a legacy system upgrade, thereby safeguarding their investments in machinery.
Support and Maintenance Considerations
The longevity and operational efficiency of refurbished CNC lathes and milling machines are heavily dependent on the availability of ongoing support and maintenance. Ensuring serviceability is a priority for these sophisticated pieces of machinery, and operators require the reassurance of continuity and peace of mind that comes from reliable support systems. One of the key concerns when it comes to refurbished equipment is the ease of access to spare parts and the expertise of suppliers in providing timely and effective support. The serviceability of these machines is not only about fixing issues when they arise but also about preventing potential problems through regular maintenance and care.
In the realm of CNC maintenance support, it is imperative that operators have access to a wide range of resources, including technical assistance and replacement parts that are compatible with their machinery. This is vital in minimizing downtime and maintaining productivity levels. Furthermore, there should be a structured system for operator training resources to ensure that those handling the equipment are well-versed in its complexities and can perform necessary upkeep tasks. This training is a pivotal aspect of equipment care and upkeep, enabling technicians to keep the machinery running at its optimal performance. Ultimately, robust maintenance support and easily accessible CNC parts availability are integral factors that contribute to the successful integration of refurbished CNC machines into a manufacturing environment.
On the same subject
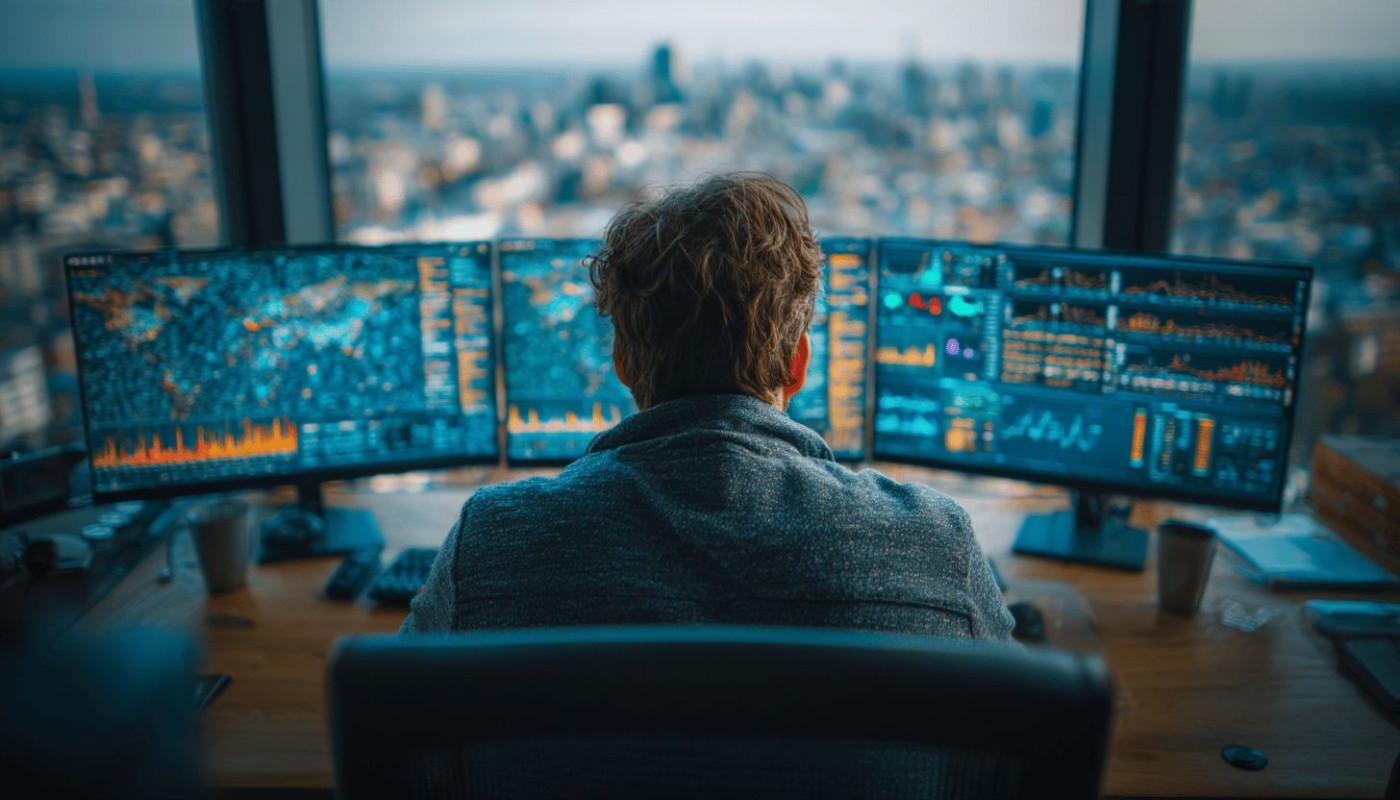
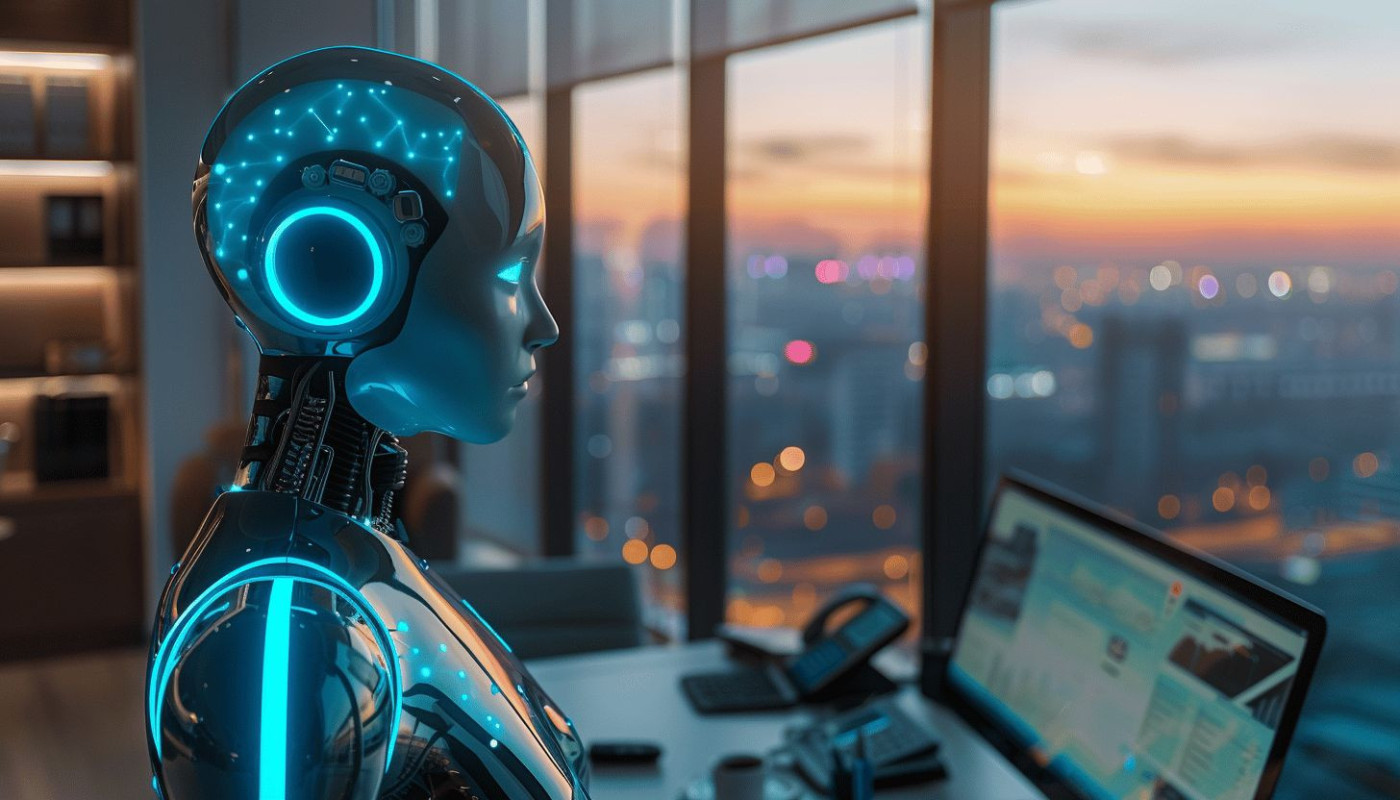
